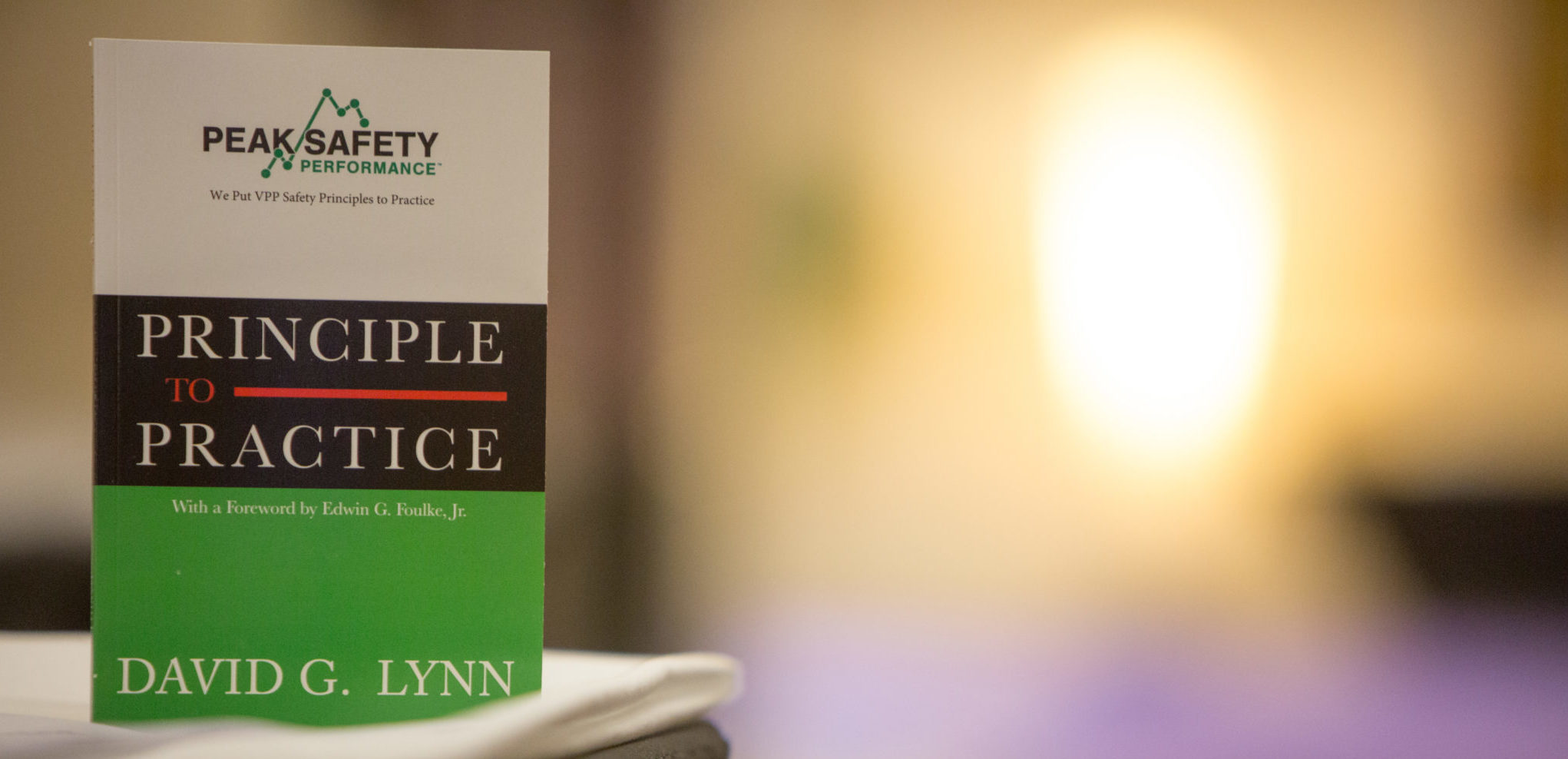
Power of Structure
The Strategic Safety Plan
The Power of Structure ASSP March 2019
I love football season. Stadium lights and fresh cut grass in the fall make me think about football. Growing up, my friends and I participated in organized leagues and we played in the backyard. The venue did not matter. Our competitive nature was evident in both settings. However, there were differences between a backyard game and a Friday night high school game. They required different levels of dedication and commitment.
When we played a “friendly” game of football in the backyard, we maintained the core philosophy of the game but our adherence to the rules was more liberal. The games were unregulated and it was the survival of the fittest. They lacked the structure and discipline that organized football requires.
Structure and discipline in organized sports taught me the finer points of the game. Coaches molded my personality. Rules taught me to appreciate fair competition. Dedication to practice enabled my success and teamwork to be molded into my character. All of these elements helped me learn to value the game and experience the rewards of my hard work. In essence, the structure of organized football created an environment with character, commitment and dedication…or a culture with clear expectations for the team.
Many companies approach safety like a backyard game where they make up the rules as they go. They have a competitive spirit but there is no discipline to the program that drives success. They lack teamwork, direction and boundaries for their program. The “backyard” safety culture does not experience the value of true dedication and hard work. However, companies can improve their own safety cultures if they recognize the difference and transition their organization to a structured team with focus and direction.
Companies with structure and discipline in their safety culture have the ability to teach employees the finer points of safety, just like organized sports. The structure molds the culture; mentors teach the value of safety and the rules help you to appreciate safety success. Commitment enables achievement and it relies on teamwork. In essence, a structured and disciplined safety program creates an evolving tradition – or a culture with clear expectations for managers and employees.
What does a structured and disciplined program look like? Successful safety cultures find a way to put fundamental safety principles into practice. They believe management commitment is important and employee involvement is essential. Professionals recognize how important it is to analyze work, put controls in place and train their employees. But, the principles are half the story. Leaders have to know how they will tactically put these principles into practice.
Just like organized sports, you have to have a game plan and strategy that puts principle to practice. The Strategic Safety Plan should include the following:
1.0 MANAGEMENT COMMITMENT AND VISIBILITY
Safety commitment does not exist without a strong and consistent management presence in the workplace. The goal for this plan is to define clear ways that the management team and supervisors can demonstrate their commitment with strategic visible action. The following management SAFE HABITS will produce SAFE WORK and positive safety results.
1.1 Daily Pre-Shift Meetings – Each area conducts a Pre-Shift meeting and safety is at the top of the agenda. These meetings are a strategic opportunity for or project Manager and the Staff to be visible in the safety discussion.
Goal: 100% management engagement! Or project Manager & Staff should monitor the quality of the safety discussion in the meetings and they should provide input for how to make the topics proactive and effective.
1.2 Weekly Safety Audits – The audit strategy should focus on consistent participation, frequent walkthroughs, fundamental coaching, standard protocols, consistent follow through with corrective action, and performance minded accountability with results.
Goal: 100% accountability for the results! Or project Manager & Staff will participate in the weekly audits and drive the process. This is a strategic opportunity to demonstrate high expectations for results. “Repeat” audit items should carry consequences.
1.3 Incident Investigations – Or project Manager & Staff will continue to be highly engaged in the incident investigation process. For recordable accidents or severe near misses, they will participate in interviews and area walks to insure results identify all root causes.
Goal: Influence the future! Elevate visibility by participating in the details of the process such as area walks and employee interviews. Follow through with corrective action across or project is also a critical area of focus.
2.0 EMPLOYEE INVOLVEMENT
2.1 Hazard Identification – Employees need a clear method for identifying and correcting hazards. The Hazard Identification process is not just about creating a list of things for maintenance to do. The process should encourage employees to take action and correct things they control. The process should be visible and simple.
Goal: Find and fix it! Develop a Hazard Identification process that focuses on what employees can control. Use the process as a way to coach and mentor employees to look for and correct risk.
2.2 Safety Teams – The safety teams should report through a formal structure. Establish a Safety Steering Team that manages the different Safety Committees. The goal for the SST is to direct, monitor, and support the Safety Committee structure. ALL team activities should focus on safety performance improvement. They should a strategy that includes a list of prioritized projects.
Goal: 100% employee engagement! Develop a structured Safety Team organization that meets consistently and they address safety performance problems strategically. Get employees involved with the solutions.
2.3 Approaching Others – ALL employees need to feel comfortable approaching others about safety hazards. This is one of the most important elements that a program can have. Once people actively help each other in the area of safety, performance begins to improve.
Goal: Protect each other! Develop a 12 month strategy for how or project will promote the Approaching Others idea. The strategy should include training, communications, and consistent face to face promotion.
3.0 WORKSITE ANALYSIS
3.1 Audits – The site currently has multiple methods for auditing work. There is an opportunity to look at all methods and streamline them into an effect overall process. The safety audit strategy should focus on consistent participation, frequent walkthroughs, fundamental coaching, standard protocols, consistent follow through with corrective action, and performance minded accountability with results.
Goal: Audit things that impact compliance and performance! Or project Manager & Staff will participate in the weekly audits and drive the process. All layers of the organization should participate. See leading indicator table at the beginning of the plan.
3.2 Incident Investigations – Every incident investigation should focus on how to influence the future and focus LESS on how to punish the past. A good investigation program identifies root causes and it provides recommendations for eliminating the hazards. Good investigators have root cause training and they utilize the skill often.
Goal: Equip people with the tools to do good investigations! Insure that the team is investigating near misses and recordable accidents.
3.3 Pre-Task Planning – One of the most effective ways to prevent accidents is to teach people to anticipate the risk. Good pre-task planning requires employees to think through the steps of a job, identify potential injuries, and put preventive measures in place.
Goal: Get employees to think “What if?” Develop and implement a formal Pre-Task Planning process. The initial process will focus on maintenance related work and projects.
4.0 TRAINING & COMMUNICATION
4.1 New Hire Orientations – This is the only opportunity that you get to make a first impression. The process should deliver information that covers regulatory requirements and it should provide relevant safety information. The delivery method should include instructor lead elements as well as video support. Participants should also take a comprehension test.
Goal: Make a positive safety impression! Have senior leaders express their commitment to safety in the orientations. Give tours if possible and make sure employees know the basic safety requirements.
4.2 Regulatory Training – Maintain an annual regulatory training schedule that includes all required OSHA training. The delivery method should include instructor lead elements as well as video support. Participants should also take a comprehension test. When possible, utilize subject matter experts for the training and/or a safety professional. If that is not possible, conduct trainer the trainer sessions with employees that will conduct the training.
Goal: Deliver good material effectively! Employees need to comprehend the topics so that they can apply the principles.
4.3 Safety Leadership Training – Great programs equip all levels of the organization to perform day to day safety related task. Safety Leadership training should teach Department Managers, Coordinators, and Team Leaders topics such as but not limited to; Why Safety is Important, Safety Responsibilities, Pre-Planning Techniques, Hazard Identification, Communication Skills, and Root Cause Analysis.
Goal: Teach leaders how to make a huge impact on safety! Establish a schedule and agenda for conducting SLT training consistently throughout the year. Anyone that directs employees should go through the training.
5.0 PREVENTION AND CONTROLS
5.1 Strategic Safety Plan – A Strategic Safety Plan defines how and what you want to do improve safety performance. The plan should include SAFE HABITS that produce SAFE WORK. The plan should also provide quantitative ways to measure performance.
Goal: Plan your success! To experience Peak Safety Performance, you have to identify the path you will take and drive progress. The plan should be on paper and should be easy to track progress.
5.2 Rules & Programs – OSHA requires companies to have specific programs and rules in place. Employees should know what they area and they should be enforced consistently. Compliance with programs and rules are a measuring stick for safety commitment.
Goal: Follow and enforce the rules relentlessly! Evaluate current “Absolutes” and determine if they are aligned with the direction or project wants to take. Make appropriate changes and create an “Absolute Pathway” for compliance to the rules.
5.3 Corrective Action Programs – Establish a process to track all open items for incidents. Assign target dates, responsibility, and monitoring expectations.
Goal: Eliminate the issue! Or project Manager & the Staff should meet at least monthly to discuss corrective action follow through. They will also evaluate how well corrective action measures were implemented and sustained plant-wide.
Putting safety principles to practice represents the structure and discipline required to succeed. This is how an organization demonstrates their commitment to safety. A structured plan establishes a positive culture with shared attitudes, values, goals and practices that characterizes a company’s reputation. The applied principles are the difference between a backyard ballgame and an organized team. Every employee has the obligation to understand these principles and make them highly visible throughout the organization. Cultures rely on the collective influence of every individual to support the team.
I challenge you to champion the cause in your work environment. Your commitment to your culture today influences tomorrow’s result